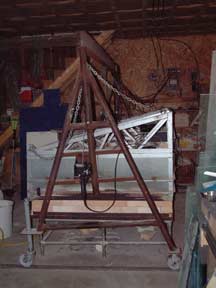
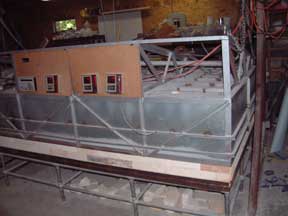
Instead of rolling my floor as many people have done, I roll my bell. You can't see by the pictures, but the bell is stabilized using 4 chains. 2 are longer, so when the bell is lowered on the chains, it swings over and contacts the A-frame gantry and becomes stabile. I can then roll the whole rig by myself back and forth. I have enough room to walk around the floor 360º
The design features that I like are that my A frame gantry is simpler to build than Nelson's structure, and I don't have to roll my floor with glass set up on it. Another feature is that I have a leveling system that allows me to adjust the height of the kiln floor from many central and perimeter points. This could not be done if the floor moved.
I have a bundle of welding cables that go from the Bell over to my switches that are mounted on the wall nearby. I got these cable holders from the electric supply that clamp on to the cables so that they don't effect the hot connections when the kiln is being moved. My rig is now 13 years old and working very well.
An alternative that I see as being acceptable would be simply lifting the bell up and down in a setting with a high enough ceiling. There needs to be a way to positively support the bell when lifted as one would not like it to fall on your head. If that support system is attached to floor and ceiling, you could avoid needing all of the cross pieces that Nelson has used.
A lively discussion on kiln design would be welcomed by me. I am working on putting together a publication with drawings and pictures. I can viusualize the same essential design working on any size from tiny to gigantic with reasonable engineering modifications.