Page 1 of 1
Drilling holes in Molds
Posted: Mon Jun 18, 2012 4:27 pm
by Marz
So, I slumped into a new circular plate mold for the first time and ended up with what looks like voids on the bottom. Someone suggested that what might have happened is that the middle of the glass slumped first, and blocked off the air hole, the edges sealed and the remaining air got pushed to the sides and formed the voids I am now seeing.
So I have two questions:
1. Can I just drill extra air holes in the sides to prevent this from happening again and how should I go about drilling these holes
2. Any thoughts or suggestions for reslumping these plates.
Thanks
Dave
Re: Drilling holes in Molds
Posted: Mon Jun 18, 2012 5:05 pm
by Brad Walker
My guess is that either your current air holes were blocked with kiln wash or you fired too high and the glass slid down and caused the bubbles you're seeing. What was the firing schedule you used?
To answer your questions:
1. Yes, you can drill more holes. Use the smallest bit you can find and drill slowly to minimize chipping.
2. it won't hurt to try, but reslumping probably won't fix the problem. Instead, you have to fire the piece flat, then slump again.
Re: Drilling holes in Molds
Posted: Mon Jun 18, 2012 11:40 pm
by Marz
Brad,
Thanks for your thoughts. I know that the air hole wasn't blocked because just before it was fired someone noted that the hole was plugged and we fixed that. I don't have the firing schedule since these were done at a local glass school. (long story)
I've included a couple of pics (at least I am going to try to anyways) to show you what I am seeing. Also, you suggested refiring the pieces flat and then reslumping. Do you think there will be any problems since I have the copper inclusion in these plates?
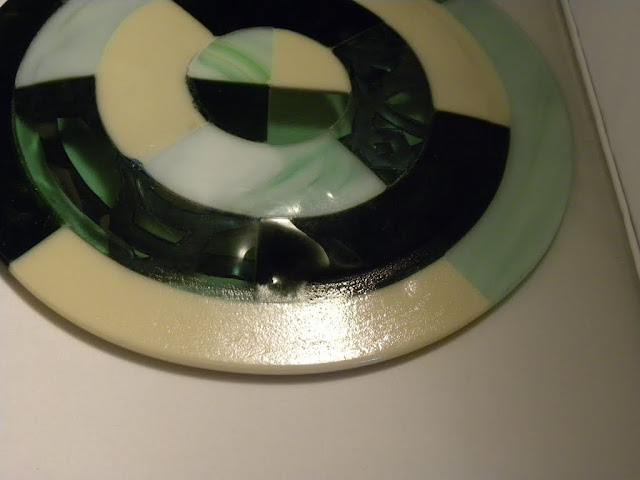
Re: Drilling holes in Molds
Posted: Mon Jun 18, 2012 11:48 pm
by Brad Walker
After seeing the photos I think that it looks similar to bubbles that form when a kiln shelf is uneven and gas gets trapped between the piece and the shelf. I've seen that happen on molds, those it's not as frequent. The problem occurs when the firing is too fast above 1100F, especially above 1300F. Without a schedule it's hard to know if that was the case here.
Anyway, I'm not sure that refiring will help much, but if you try I would go slowly due to the inclusions and the time you've already spent on the piece.
Be interested to know if anyone else has any thoughts.
Re: Drilling holes in Molds
Posted: Tue Jun 19, 2012 12:17 am
by Brock
Those copper inclusions look pretty thick. What gauge are they?
Re: Drilling holes in Molds
Posted: Tue Jun 19, 2012 2:30 am
by Morganica
The shape makes me kinda wonder--do the holes line up with the copper inclusions at all? Asking because a friend got much the same thing on a flat kilnshelf about a month ago, using copper inclusions. Really weird, but it flattened out just fine on the next firing.
Re: Drilling holes in Molds
Posted: Tue Jun 19, 2012 9:35 am
by Marz
The copper is .004" thick. There is only one hole in the center of the mold.
Re: Drilling holes in Molds
Posted: Tue Jun 19, 2012 4:17 pm
by Susan B
It may just be that there are copper inclusions.
I purchased a flat panel which has copper inclusions.
It is two layers of glass thick with the copper in between.
The top of the panel dips down into the "empty holes" of the copper pattern and down again around the edges of the inclusions.
By the same token, on the bottom of the panel, the glass has pulled up away from the shelf, where the top layer is dipping down.
Re: Drilling holes in Molds
Posted: Thu Jun 28, 2012 9:17 pm
by Thomas Decker
I have had the same problem with a shallow mold like this there is no need to go any higher than 1200 degrees I did fix the problem a little by drilling more holes but have still had a problem if I go beyond the 1200 point the glass covers the holes and the bubbles form 1150 degrees works even better.