Keeping a Firing Log
A properly kept firing log is essential to keep track of what you’ve done.
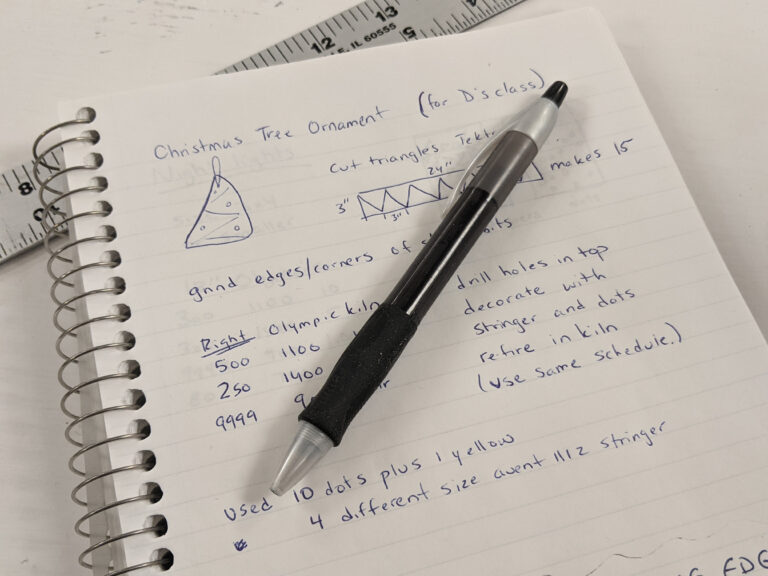
In many ways the firing log is the most under appreciated warm glass tool. All too often, the eagerness to fire overcomes the need to keep records of the firing, resulting in loose scraps of paper with illegible writing, disorganized rambling, or generally useless comments.
This is a huge mistake. The firing log is one of the most important tools you have. The combination of your kiln, the glass you select, and the designs you create are unique to you. No one else can precisely duplicate the conditions in your kiln, so it’s up to you to keep records that are detailed enough to allow you to repeat good firings and avoid repeating bad ones.
Keep a notebook in your work area. Use it religiously and enter essential information about each firing.
- Date and time of firing.
- Type of firing. Possibilities include slumping, fusing, kiln casting, and fire polishing. Include information about the item being fired (bowl, plate, etc.).
- Type of glass. Enter brand, whether opalescent, cathedral, or mixed, and any other significant features of the glass being used. Identify unusual textures.
- Firing schedule details. Include enough information to allow you to duplicate this firing completely. If your kiln has a controller, write down the program you used. Document each phase of the firing.
For each phase, it’s a good idea to enter the temperature at the start of the phase, the temperature at the end of the phase, how long it took to complete the phase, and whether or not you soaked at the end of the phase. You may want to enter the firing time for the phase as a length of time (e.g., two hours) or as a rate of temperature change (degrees per hour). Use either method, but be sure to enter the information.
As important as it is to keep a record of the firing schedule, it’s even more important to make comments about the success or failure of the firing. What went well? What do you want to avoid the next time?
Your comments might include:
- Any cracking. If the glass cracked, indicate the kind of crack, the number of cracks, and whether it split into pieces.
- Nature of edges. Are they smooth and well formed or uneven and irregular?
- Degree and type of bubbles. How many, how large, probable cause?
- Placement of item in kiln. Was it centered or close to the edge, was it closer to the elements than normal?
- Fiber paper or kiln wash. Each fires differently. If you normally fire on kiln wash but used fiber paper this time, then record the difference.
- Type of mold used. Stainless steel, ceramic, wet felt, all can cause the item to behave differently.
- Uneven slumping. Did the item lurch to one side or the other?
- Any devitrification or other discoloration. Did the glass devitrify? Did it change color or behave unexpectedly?
- Opened kiln. Document the opening of the kiln to vent during initial heating or to accelerate cooling. Don’t forget to mention how far the kiln was opened.
- Apparent hot spots. Does one part of the kiln appear to be hotter or colder than other parts?
- Other unusual events. Anything that happened during the firing that seems out of the ordinary. Document power outages, earthquakes, or unexplained results.
Rather than being a hindrance, a firing log can be viewed as the warm glass artist’s best friend. It’s the place to document what happened and why. Document your experiences and your theories.
As you become more experienced, you may find that many of your firings are similar and require little (or even no) entries. But regardless of your experience level, your firing log can be used as an invaluable tool in helping you learn and document the intricacies of your kiln and the glass you use.