What are the different kinds of glass?
What kind of glass can you use?
And what are the differences between types of glass?
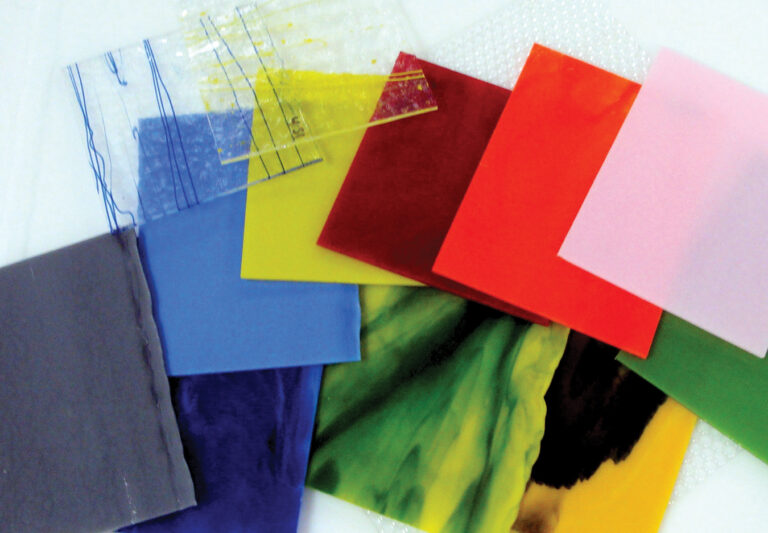
You can use any glass for fusing and slumping, but some glass works better than others. Even ordinary window glass (called “float” glass by people in the field) can be used, although most people prefer colored glass like that used in stained glass work.
It’s likely that you will want to combine more than one different sheet of glass in your projects. If so, then you’ll need to make sure the glass you select is “compatible.” Compatibility is a way of saying that the difference pieces of glass you use expand and contract at similar rates. Using incompatible glass may cause cracking or even shattering of the piece when it cools.
In addition to compatibility, glass artists also differentiate among different types of glass in many different ways. One of the major criteria for differentiation is the transparency of the glass. Opaque glasses that do not transmit light are generally referred to as “opaques”, as “opalescent” glasses, or as “opals.” See-through glasses of various colors are usually called “transparent” or “cathedral” glasses. Combining more than one different opalescent or cathedral glass or color in a single kiln-formed work is common.
In addition to compatibility, glass artists also differentiate among different types of glass in many different ways. One of the major criteria for differentiation is the transparency of the glass. Opaque glasses that do not transmit light are generally referred to as “opaques”, as “opalescent” glasses, or as “opals.” See-through glasses of various colors are usually called “transparent” or “cathedral” glasses. Combining more than one different opalescent or cathedral glass or color in a single kiln-formed work is common.
Several different companies offer lines of tested compatible glass, with the largest and most popular being Bullseye and Oceanside/Spectrum. Many other firms, including companies such as Armstrong, GNA, Kokomo, Wissmach, and Youghiogheny, also manufacture glass that is sometimes used in fusing. Sometimes Sometimes the glasses made by these companies tests compatible for fusing, but often it does not. If you wish to use any of these glasses for kiln-forming projects involving more than a single sheet of glass, you will need to test for compatibility.
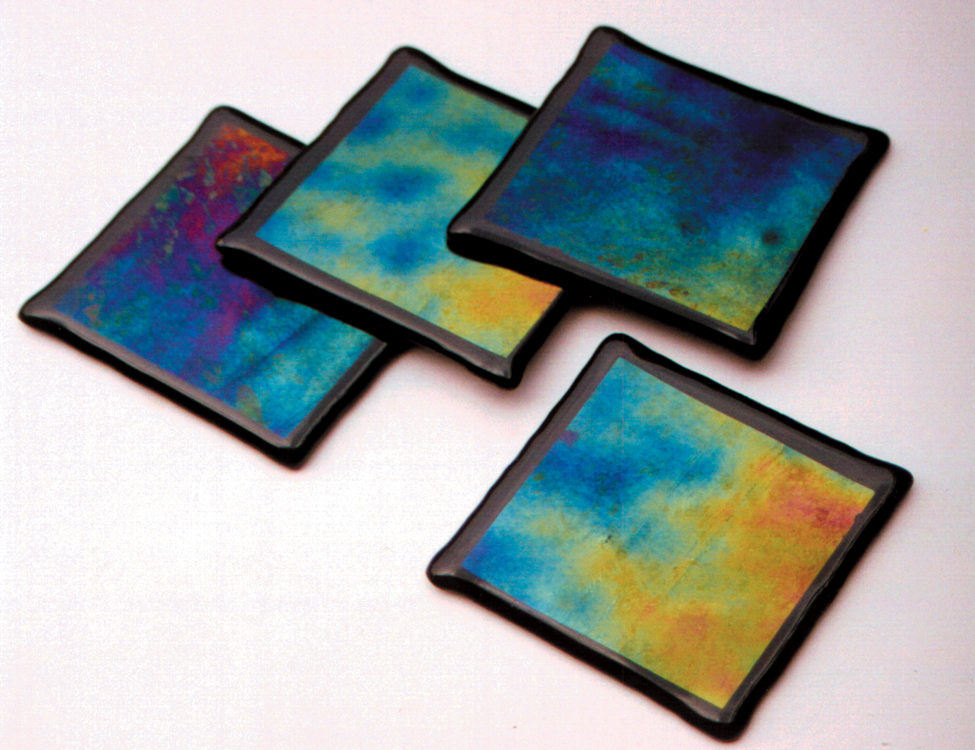
Virtually any stained glass, whether tested compatible or not, can be treated with an iridescent coating that causes the treated side of the glass to take on a metallic sheen. Some liken this effect to a shimmering rainbow. The shimmer goes away when the piece is lit from behind, allowing the normal color of the glass to shine through.
Another popular kind of glass coating, called “dichroic”, has the unusual property of reflecting one color while it transmits another. This means that the different colors can be viewed by examining the glass at different angles. This unique glass is manufactured by spraying a thin chemical film on the glass. This must be done in a controlled environment in a vacuum chamber, making dichroic glass one of the most expensive glasses made for kiln-forming. Because of this expense, dichroic glass is more commonly used in jewelry and similar items, or as an accent in larger scale fusing projects.
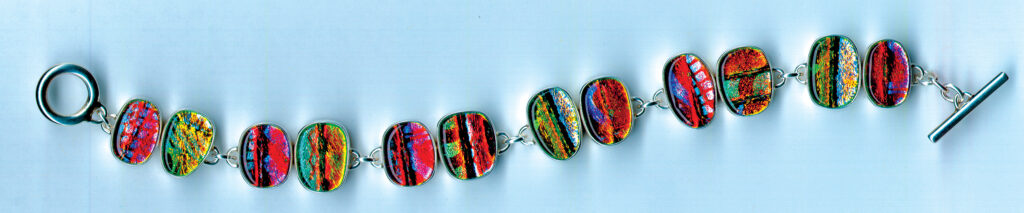

One common type of glass that can sometimes be used for kilnforming is “float” glass. Made by “floating” molten glass on a bath of molten tin, float glass is better known as common window glass. It is inexpensive and widely available. It also works well in the kiln, but care should be taken to test for compatibility if different brands and types of float glass are mixed together. If at all possible, cut pieces to be fused together from the same glass sheet.
Although some colored varieties of float glass are available, it is most commonly found in a clear (often slightly greenish) formulation. It tends to slump and fuse at slightly higher temperatures than most art glass (about 75 to 100 degrees F higher), and can be prone to devitrification. Its COE depends on the specific formulation used and can be as low as 83 or as high as 90, but it generally ranges from 85 to 87.
And, finally, it is possible to use ordinary wine or beer bottle glass in the kiln. Typically, bottles are flattened on the kiln shelf or inside a mold. This process is known as “bottle slumping.” For best results, don’t fuse bottles together (they’re likely to be incompatible) and don’t fire bottle glass too many times or to too high a temperature (that can cause them to stiffen or to lose their shine).